
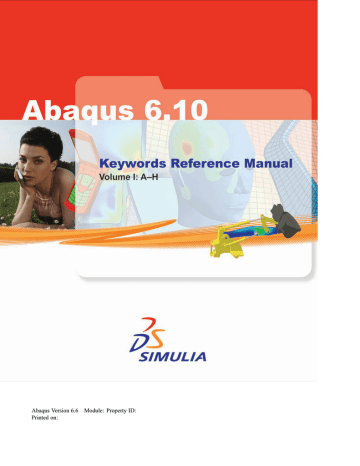
This scale has the advantage of being able to obtain both global results, such as reinforcement in the deformed state, and local results, such as yarn deformations or yarn cross-shape evolution. The mesoscopic scale is the intermediate scale between the two previous scales and considers the intertwining of supposedly continuous yarns. Several methods for simulating the reinforcement shaping exist, depending on the scale of the study. Therefore, it is important to supplement them with numerical methods. Experimental methods allow obtaining direct and effective results, but their implementation is frequently long, difficult, and limited to existing reinforcements. There are two possibilities for studying dry reinforcement deformations. This work addresses the injection process of the LCM family, specifically, the resin transfer moulding (RTM) process where the preforming is a key stage in the production of composite parts. Among the processes used for the application of composites, we can distinguish between technologies using thermosetting matrices (draping of prepregs and the liquid composite moulding (LCM) process family) from those based on hot forming of thermoplastic matrix plates. Carbon fabric is one of the reinforcements that is receiving significant attention for its potential use in aircraft structures,. Recently, with the rapid development of automotive and aerospace industries, woven carbon has become a good candidate material for use in these high-performance domains. Understanding the behaviour of woven composite fabrics is critical to achieving the ultimate goal, in this context, we investigated the effect of some forming process parameters on the shear angle values of the final deformed shape. The results show that the non-linear tensile behaviour is better correlated with the hybrid hypoelastic model than with the hybrid elastic model, which can explain the importance of considering the non-linearity in the tensile test and shear behaviour.
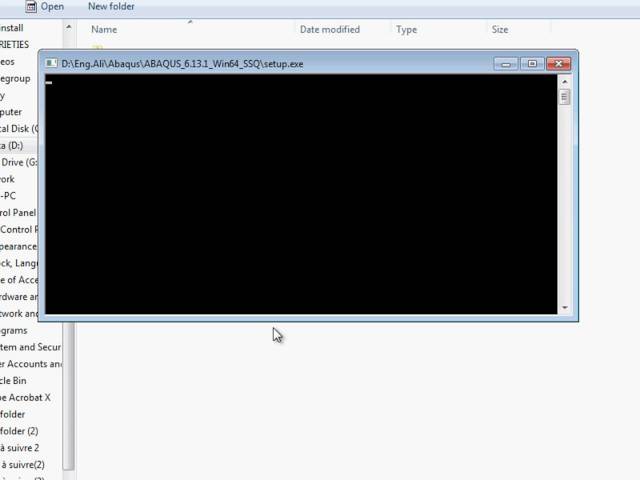
The developed model is able to predict the initial phase during tensile loading, where threads tend to straighten and flatten.

The model is validated through a comparison between numerical and experimental results. The difference between the two models lies in the in-plane shear behaviours, which is linear elastic in the first model and hypoelastic in the second and can track the material orientation especially in large deformations. In both hybrid models, connectors for tensile behaviour are combined with membranes for consideration of the in-plane shear. Two hybrid discrete continuous approaches based on mesoscale modelling are developed and implemented in the Abaqus software using VUMAT subroutines. In this study, the behaviour of woven composite fabrics under large deformation is investigated.
